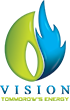
Low-density polyethylene
Low-density polyethylene (LDPE) is a thermoplastic made from the monomer ethylene. It was the first grade of polyethylene, produced in 1933 by Imperial Chemical Industries (ICI) using a high pressure process via free radical polymerization.[1] Its manufacture employs the same method today. The EPA estimates 5.7% of LDPE (recycling number 4) is recycled.[2] Despite competition from more modern polymers, LDPE continues to be an important plastic grade. In 2013 the worldwide LDPE market reached a volume of about US$33 billion.[3]
Properties[edit]
LDPE is defined by a density range of 0.917–0.930 g/cm3.[4] It is not reactive at room temperatures, except by strong oxidizing agents, and some solventscause swelling. It can withstand temperatures of 80 °C continuously and 90 °C (194 °F) for a short time. Made in translucent or opaque variations, it is quite flexible and tough.
LDPE has more branching (on about 2% of the carbon atoms) than HDPE, so its intermolecular forces (instantaneous-dipole induced-dipole attraction) are weaker, its tensile strength is lower, and its resilience is higher. Also, because its molecules are less tightly packed and less crystalline due to the side branches, its density is lower.
When exposed to ambient solar radiation the plastic produces two greenhouse gases, methane and ethylene. Due to its low density properties (branching) it breaks down more easily over time, leading to higher surface areas. The production of these trace gases from virgin LDPE increase with surface area/time, with rates at the end of a 212-day incubation of 5.8 nmol g-1 d-1 of methane, 14.5 nmol g-1 d-1 of ethylene, 3.9 nmol g-1 d-1 of ethane and 9.7 nmol g-1 d-1 of propylene. When incubated in air, LDPE emits gases at rates ~2 times and ~76 times higher in comparison to water for methane and ethylene, respectively.[5]
Chemical resistance[edit]
• Excellent resistance (no attack/no chemical reaction) to dilute and concentrated acids, alcohols, bases and esters
• Good resistance (minor attack/very low chemical reactivity) to aldehydes, ketones and vegetable oils
• Limited resistance (moderate attack/significant chemical reaction, suitable for short-term use only) to aliphatic and aromatic hydrocarbons, mineral oils, and oxidizing agents
• Poor resistance, and not recommended for use with halogenated hydrocarbons.[6]
Applications
LDPE is widely used for manufacturing various containers, dispensing bottles, wash bottles, tubing, plastic bags for computer components, and various molded laboratory equipment. Its most common use is in plastic bags. Other products made from it include:
• Trays and general purpose containers
• Corrosion-resistant work surfaces
• Parts that need to be weldable and machinable
• Parts that require flexibility, for which it serves very well
• Very soft and pliable parts such as snap-on lids
• Six pack rings
• Juice and milk cartons are made of liquid packaging board, a laminate of paperboard and LDPE (as the waterproof inner and outer layer), and often with of a layer of aluminum foil (thus becoming aseptic packaging).[7][8]
• Packaging for computer hardware, such as hard disk drives, screen cards, and optical disc drives
• Playground slides
• Plastic wraps