ASPC LIM1922
LIM1922 is recommended for injection molding process. This product is injected for producing flexible injection molded articles such as toys, household articles, caps, lids and as base resin for master batches.
LFI2185A has been manufactured using SABTEC licensed technology.
Extruder temperature profile: 175-190°C
Frost line height: 5-7 times die diameter.
Blow Up Ratio: 2-4
Recommended film thickness: 45 to 100 μm.
Please note that, these processing conditions are recommended by producer only for 100% LFI2185A resin (not in the case of blending with any other compatible material), but because of the many particular factors which are outside our knowledge and control, and may affect the use of product, no warranty is given.
Supplied in pellet form and can be packaged in 25kg Bags, one ton semi bulk or 17 tons bulk containers.
Food Packaging
The above mentioned grade meets the relevant requirements of plastics directive 2002/72/EC (06-08-2002) and its amendments till directive 2008/39EC relating to plastic materials and articles intended to come into contact with foodstuffs.
Pharmaceutical Application
The above mentioned grade meets the requirements of the European pharmacopeia version 6 sections 3.1.5 for pharmaceutical application.
Conveying
Conveying equipment should be designed to prevent accumulation of fines and dust particles can, under certain conditions, pose an explosion hazard. We recommend that the conveying system used:
1.Be equipped with adequate filters.
2.Is operated and maintained in such a manner to ensure no leaks develop.
3.That adequate grounding exists at all times.
We further recommend that good housekeeping will practiced throughout the facility.
Storage
All resins should be protected from direct sunlight and/or heat during storage. The storage location should also be dry, dust free and the ambient temperature should not exceed 50°C. It is also advisable to process polyethylene resins (in pelletized or powder from) within 6 months after delivery, this because also excessive aging of
polyethylene can lead to a deterioration in quality. ASPC would not give warranty to bad storage conditions which may lead to quality deterioration such as color change, bad smell and inadequate product performance. It is also advisable to process polyethylene resins (in pelletized or powder form) within 6 months after delivery, this because also excessive aging of polyethylene can lead to a deterioration in quality.
Handling
Minimal protection to prevent possible mechanical or thermal injury to the eyes. Fabrication areas should be ventilated to carry away fumes or vapors.
Combustibility
Polyethylene resins will burn when supplied adequate heat and oxygen. They should be handled and stored away from contact with direct flames and/or other ignition sources .in burning; polyethylene resins contribute high heat and may generate a dense black smoke. Fires can be extinguished by conventional means with water and mist preferred. In enclosed areas, fire fighters should be provided with self-containedbreathing apparatus.
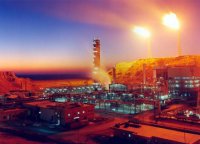
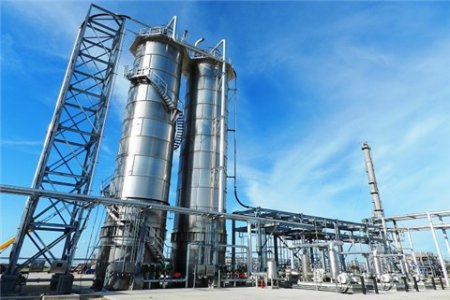
Properties |
Value (1) |
unit |
Test method |
Polymer Properties |
|
|
|
MFI (190 0C /2 .16 Kg ) |
22 |
dg/min |
ISO 1133 |
MFI (190 0C /5 Kg ) |
75 |
dg/min |
ISO 1133 |
MVR (190 0C /2 .16 Kg ) |
29 |
ml/10min |
ISO 1133 |
MVR (190 0C /5 Kg ) |
98 |
ml/10min |
ISO 1133 |
Density |
919 |
Kg/m3 |
ISO 1183 (A) |
Thermal Properties(2) |
|
|
|
Heat deflection temperature at 0.45MPa |
39 |
°C |
ISO 75 |
(HDT/B) |
|
|
|
Vicat softening temperature at 10N (VST/A) |
82 |
°C |
ISO 306 |
Melting Point |
105 |
°C |
ASTM D 3418 |
Enthalpy change |
104 |
j/g |
ASTM D 3417 |
Mechanical properties(2) |
|
|
|
Stress at yield |
8 |
MPa |
ISO 527-1/2 |
Stress at break |
7 |
MPa |
ISO 527-1/2 |
Strain at break |
400 |
% |
ISO 527-1/2 |
Tensile modulus |
175 |
MPa |
ISO 527-1/2 |
Creep modulus (After 1 hour) |
80 |
MPa |
ISO 899-1 |
Creep modulus (After 1000 hour) |
45 |
MPa |
ISO 899-1 |
Notched lzod at +23°C |
42 |
KJ/m2 |
ISO 180 A |
Notched lzod at -30 °C |
5 |
KJ/m2 |
ISO 180 A |
Notched Tensile impact strength |
86 |
KJ/m2 |
ISO 8256/1B |
Elongation at break |
8.4 |
% |
ISO 8256/1B |
Maximum Tension |
16 |
MPa |
ISO 8256/1B |
Hardness Shore D |
45 |
- |
ISO 868 |
Ball indentation test |
|
|
|
Applied load |
49 |
N |
ISO 2039-1 |
Ball indentation hardness |
16 |
MPa |
ISO 2039-1 |
ESCR |
3 |
h |
SABTEC |
|
|
|
Method |
Additive : Antioxidant |
|
|
|
Notes:
(1)Typical Values: not to be construed as specifications limits.
(2)Properties are based on 45 μm blown film produced at a melt temperature of 190°C and 3 BUR using 100% LTM 2185/47.
Note: this information is based on our current knowledge and experience .in view of many factors that may affect processing and application, this data does not relive processors from the responsibility of carrying out their own tests and experiments, neither does it imply any legally binding assurance of certain properties or of suitability for a specific purpose. It is the responsibility of those to whom we supply our products to ensure that any proprietary rights and existing laws and legislation are observed.
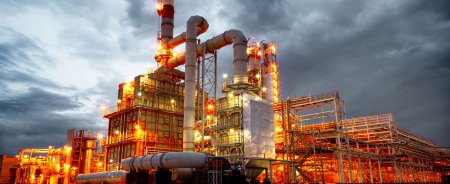